EP Plastic Self-lubricating Bearings
- EP Plastic Self-lubricating Bearings EP series of high-performance engineering plastic polymer bearings as the base material, through modification of polymer materials technology into high-strength fibers and specialty solid improvement in its internal grease integrated wear resistance; high strength fiber reinforced network structure strength of the material, the composite solid special grease allows EP series plastic bearings with excellent self-lubricating properties and wear resistance. Whether it is a high durability requirements the automotive industry.
TechnologyMaterialEPTEPGEPHEPXEPJEPS
Engineers are dedicated on the performance improvement on the self- lubricating materials derives the result that EP Series Materials are with excellent self- lubricating features and wear resistance Features. High- strength fibers used in the engineering plastics fantastically improve the material load(Graph1). Special grease immersion in the plastic can decrease the friction coefficient of the material therefore to proiong the bearing sevice life. High- performance engineering plastics body material mainly service as wear- resistant vector. The reinforced fiber improves the load and impact resistant capacity of the bearing. Special grease decreases the fricton coefficient for a better self- lubricating performance.
Graph1 EP inner structure
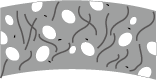
Because the grease immersed in the solid plastic material, the lubricating will be valid continuously no matter how long the bearings are working. Therefore, the traditional sintered oilless bearings provide the lubricating function by utilizing the impregnated oil in the tiny porosities of the material. When the impregnated oil would have been run out of dried, the bearing wear will be increased sharply and the bearing life will be terminated at the same time. (Graph 2).
Graph2 Surface wear

Plastic bearing has longer service life

Lubricating oil is easy to be failed
The self-lubricating feature of the EP bearing is achieved by adding solid lubricants and functional fibers into the body material and the friction coefficient is decreased by the soild lubricate grease immresion. The friction coefficient is affected by the load, operating speed and shaft roughness. The friction coefficient is generally decreased along the load increasing and increased along the operating speed(see Graph3). Please refer to Gragh 3 for the relation between the friction coefficient and shaft roughness.
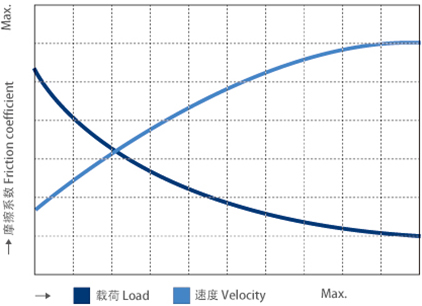
Slightly wear off will occur as soon as the self-lubricating bearing is applied with a certain load. It is the same to the EP series bearings, when the slightly wear occurs, the immersed oil (grease) will infiltrate out from the bearing filling the wear off area of the bearing as well as the mating material to form the lubricating film (Gragh 4) ang therefore interrupt the wear process. In this way, the aforementioned working method of the plastic bearings improves the wear resistance feature of the bearings and maintain the further operation stable (Gragh 5).
Gragh 4: After operation, lubricating oil film formed

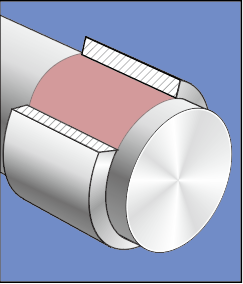
Gragh 5: Wear against operaton time
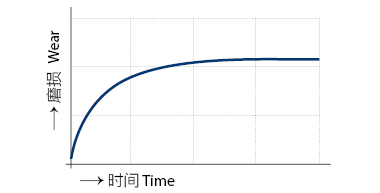
■ Load capacity calculation
◇ Cylidrncal bushes, flange bushes
P= F / d×L (N/mm²)
F=Load (N)
d=Shaft (mm²)
L=Bearing Length (mm²)
◇ Thrust washer
P= 4F / π(D2-d2) (N/mm²)
F=Load (N)
D=Washer OD(mm²)
d=Washer ID(mm²)
As the factor of clearance, bushes chamfer, oil groove ect, The actually load ( Pact) is higher than theory of calculation(Pmean).
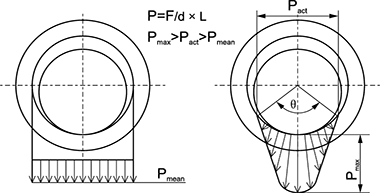
■ Maximum surface static load
The actual dynamic load is usually less than the maximum surface static load recommended in the data sheet. Due to the clearance exists between the shaft and bearings, the actual working surface area are not the same as the projected area of the bearing, The working area is depended on the clearance between the shaft and the bearing. The value in the datasheet is valid when the shalt is less than 0.01m/s. The value could also be applicable for a short run (shorter than 3 minutes) condition.
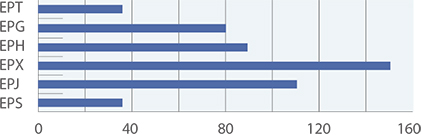
■ The load, temperature and speed
The load capacity will be decreased along with the
temperature increase. Load capacity may sharply
decrease when the operating temperature is higher than
the recommended maximum temperature (Graph 7).
The load capacity will be decreased along with the speed
increase. Speed increase will result into a temperature
increase that decreases the load capacity.
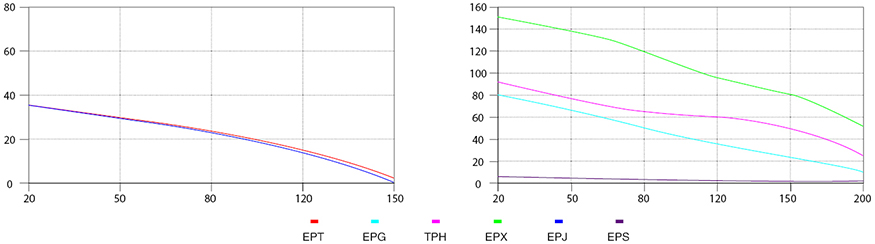
■ Calculation of Linear Speed
◇ Rotating motion
V=π×d×n / 1000×60 (m/s)
d=Shaft (mm²)
n=Rpm
◇ Oscillationg motion
V= π×d×C×θ / 1000×360×60
d=Shaft (mm²)
C=Frequency
θ=Oscillating angle
◇ Reciprocating motion
V=π×d×n / 1000×60 (m/s)
S=Stoke distance (m)
C=Frequency
The maximum operating speed: Rotation, Oscillating, Linear indicates the maximum allowable speed (Graph 8). The value in the datasheet is calculated under the condition of a very low load. So the actual allowable speed will be limited against different load and other conditions. The higher the load, the lower the speed will be. The speed and the temperature is in a inverse proportion relation, the maximum speed allowable will be different depending on different operation method of the bearings.
Graph 8: Max Operating SpeedMaterial | Rotation | Oscillating | Linear |
EPT | 0.1 | 0.7 | 3.0 |
EPG | 1.0 | 0.7 | 4.0 |
EPH | 1.0 | 0.7 | 3.0 |
EPX | 1.5 | 1.1 | 5.0 |
EPJ | 1.5 | 1.1 | 8.0 |
EPS | 2.0 | 1.4 | 5.0 |
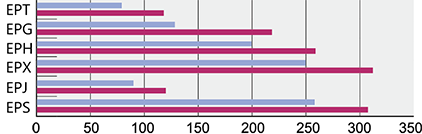
There is a limited temperature range that EP Series bearings could be used. The lowest temperature is the one the material will become brittle under that value (Graph 10) and the highest temperature is the one the bearing material wear resistance feature will start to change (Graph 9). If the bearings are used under the conditions of alternatively changing high and low temperature, the bearing feature will be considerably affected and thus shorten the bearing service life.
Graph 10: Min Operating TemperatureMaterial | Min Temperature |
EPT | -40 |
EPG | -40 |
EPH | -40 |
EPX | -100 |
EPJ | -50 |
EPS | -200 |
Material | Min Temperature |
EPT | -40 |
EPG | -40 |
EPH | -40 |
EPX | -100 |
EPJ | -50 |
EPS | -200 |
PV is the product of the specific bearing load P and the sliding speed V. It is a very important design data for the bearing application. The PV value is inverse proportional to the bearing sevice life ( Graph 12).So it is recommended to consider a lower design PV value during the bearing the bearing selection.
Graph 12: PV Value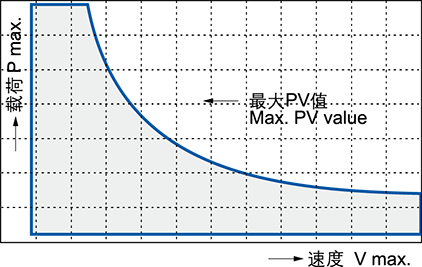
PVPerm.=(K1×π×λk×△T / μ×s) + (K2×π×λs×△T / μ×b1×2) ×y1×y2×10-3
There:
K1,K2 = Constant for heat dissipation(K1=0.5, K2=0.042)
s = Bearing wall thickness [mm²]
b1 = Bearing length [mm²]
μ = Coefficient of friction
λs = Thermal coductivity of the shaft
λk = Thermal coductivity of the bearing
△T = (Ta - Tu)
Tu = Ambient temperature [℃]
Ta = max. application temperature [℃]
Y1 = Intermittent operation correction factor
Y2 = Lubricating operation correction factor
Commonly the bearings are not continuously running during most of the applications. The short time operation period (less than 10 minutes) does not allow the bearing reach the highest limited operation temperature so that the limited PV value will increase because during the stop period, the heat generated by the friction will be reduced. Graph 13 shows the intermittent operation correction factor y1 for different stop and operate period.
Graph 13: Correction factor of PV value by Intermittent Operation
Although EP bearings are normally designed for the dry operation, it has good the general lubricant such as oil or grease. The initial oil or grease lubricating will improve the starting performance of the bearings and therefore achieves a shorter run-in time. At the same time, the using of lubricants considerably improves the loading capability of the bearings because the lubricants will reduce the temperature increasing during the operation so that the loading capability of the bearings is improved. Graph 14 shows the PV correction factor y2 for different lubricants are used.
Graph 14: Correction factor of PV value by means of lubricationLubrication | Correction factor |
Dry | 1 |
Grease | 2 |
Water | 4 |
Oil | 5 |
As the bearings wear resistance affected by many factors, it is difficult to accurately describe bearing wear and life span. Through numerous experiments we can conclude that the main factors affect the anti-wear property are the load, moving method, speed, roughness of mating surfaces, ambient temperature and dust and type of the outside lubricating medium, etc. When the load, speed and temperature increase, the wear resistance of bearings gradually reduced; when there is outside lubrication medium, the wear resistance could be doubled; SAVI recommend the roughness of axis to be Ra0.2 - Ra0.8. If the shaft is too rough or too smooth, it might increase the wear. Although there is no special restriction on the using of shaft material for the EP series bearings, SAVI recommend the use of hard chrome plated shaft material. The recommended shaft hardness is over HRC35 in order to avoid the initial wear off on the shaft.
Graph 15: Heat conductivity values of shaft or housing materialsMaterial | Thermal conductivity[W/m x k] |
Carbon steels | 46 |
Hardened steel | 46 |
Hard chrome shaft | 46 |
Stainless steel | 16 |
Hardened aluminum | 204 |
Plastic | 0.24 |
Bearings used for outdoor equipments are constantly exposed to different critical environment. Anti-UV property is one of the most important indexes of a variety of bearing materials to resist UV-ray damage. EP Series plastic bearing UV-resistance reference (Graph 16).
EP series plastic bearings are usually used under the conditions where chemical media exist. Therefore the chemical resistance feature is very important for such a critical application. The existing chemical media may cause deep changes to the performance of the bearing material depending on the different conditions such as the chemical kinds, temperature, and the contacting period to the bearing materials as well as the load and operation speed. Sometimes chemical medium act as an effective lubricant and thus will extend the service life of bearings. Resistant to virtually all chemical media (Graph 16).
Graph 16:Bearing UV-resistance vs Chemical resistance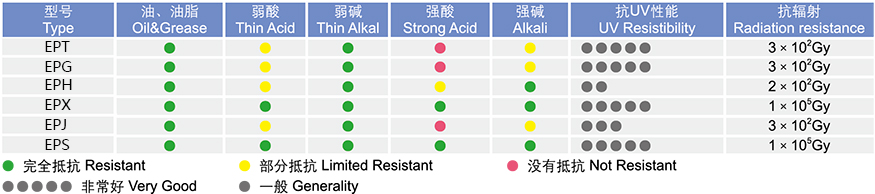
■ Housing: The bearing housing and the fitting tools must be kept clean during the assembling. A chamfer of 250 0n the housing should be ensured for an easy assembling. A stepped press pin is recommended to be used for the assembling. The inner diameter of the EP series product is measured after the bushing is fitted into the H7 housing.
Graph 17: Assembly example
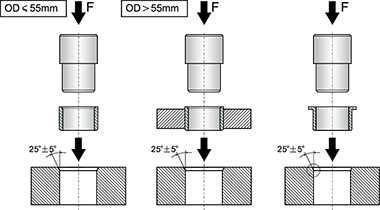
■ Shaft: There is no critical requirement for the shaft material but chrome plated shaft is recommended for better operation.
Rounded chamfer is required on the shaft for easy assembling. SAVI recommend the shaft roughness to be in the
range of Ra0.2-0.8. Please refer to Graph 15 for the relation between the surface roughness and bearing friction
coefficient(Graph :1 9).
EP series products are designed according to IS0 3547 Standard(Graph 18). Although the EP bearings
are designed for self-lubricating purpose, but the initial lubricating helps the assembling and the future operation of the
bearings.
Graph 19: Friction coefficient & surface roughness
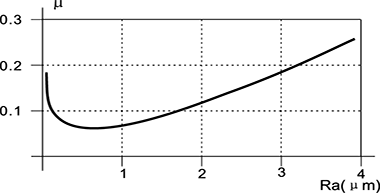
■ Adhesive agent: EP series plastic bearing assembly generally needn't use glue, in case the glue is necessary, please consider the used glue can also work properly at the required temperature. Relative testing is recommended in this case.
Graph 18: The Interfit Toleranced mm² | Tolerance after fit E10 | Fit Housing H7 | Fit Shaft h9 |
>0~3 | +0.014~+0.054 | 0~+0.010 | 0~-0.025 |
>3~6 | +0.020~+0.068 | 0~+0.012 | 0~-0.030 |
>6~10 | +0.025~+0.083 | 0~+0.015 | 0~-0.036 |
>10~18 | +0.032~+0.102 | 0~+0.018 | 0~-0.043 |
>18~30 | +0.040~+0.124 | 0~+0.021 | 0~-0.052 |
>30~50 | +0.050~+0.150 | 0~+0.025 | 0~-0.062 |
>50~80 | +0.060~+0.180 | 0~+0.030 | 0~-0.074 |
>80~120 | +0.072~+0.212 | 0~+0.035 | 0~-0.087 |
>120~180 | +0.085~+0.245 | 0~+0.040 | 0~-0.100 |
Material
Common Capability | Unit | EPT | EPG | EPH | EPX | EPJ | EPS |
Density | g/cm³ | 1.46 | 1.46 | 1.65 | 1.49 | 1.24 | |
Color | Black gray | Dark grey | Grey | Black | Yellow | Beige | |
Max.water absorption,23℃/ 50% | [% weight] | 0.2 | 0.7 | 0.1 | 0.3 | 2.02 | |
Max.water absorption | [% weight] | <1.2 | <4 | <0.3 | <0.5 | <1.3 | <0.1 |
Dynamic friction /steel | μ | 0.05-0.15 | 0.08-0.18 | 0.07-0.20 | 0.09-0.27 | 0.06-0.18 | 0.05-0.15 |
Max.PV(dry) | MPa•m/s | 0.4 | 0.5 | 1.37 | 1.32 | 0.34 | 0.4 |
Mechanical behavior | |||||||
E-module | MPa | 2,300 | 7,800 | 12,500 | 8,100 | 2,400 | 830 |
Tensile strength,20℃ | MPa | 80 | 200 | 175 | 170 | 73 | 18 |
Compressive strength | MPa | 65 | 80 | 90 | 150 | 35 | 10 |
Max.static pressure of the surface,20℃ | MPa | 35 | 80 | 150 | 90 | 20 | 10 |
Shore D hardness | 70 | 112 | 87 | 85 | 74 | 73 | |
Physical and thermal properties | |||||||
Continuous work tempreature | ℃ | +80 | +130 | +200 | +250 | +90 | +260 |
short-time work tempreature | ℃ | +120 | +220 | +240 | +315 | +120 | +310 |
Minimum operating temperature | ℃ | -40 | -40 | -40 | -100 | -50 | -200 |
Thermal conductivity | W/m•K | 0.2 | 0.25 | 0.60 | 0.60 | 0.25 | 0.24 |
Max.water absorption,23℃ | K-1•10-5 | 7 | 9 | 4 | 5 | 10 | 12 |
Conductivity | |||||||
Volume resisticity | Ωcm | >1012 | >1013 | <104 | <105 | >1013 | >1015 |
Surface resisticity | Ω | >1015 | >1011 | <105 | <103 | >1012 | >1015 |
-
-
EPT
Universal BearingsIt can meet most applications working temperature of 80 degrees below, excellent wear resistance...
READ MORE >>
-
-
EPG
High load-bearingApplications ace high loads. As the perfect combination of fiber reinforced material and lubrication.
READ MORE >>
-
-
EPH
Corrosion-resistant bearingsHigh temperature of 200 degrees and a low coefficient of friction material...
READ MORE >>
-
-
EPX
High-temperature
bearingsHigh temperature of 250 degrees of self-lubricating material. High chemical ...
READ MORE >>
-
-
EPJ
High-speed bearingsLow coefficient of friction and high wear resistance perfect combination. Rotary, linear and oscillating...
READ MORE >>
-
-
EPS
Tetrafluoroethylene modified bearingHigh-speed low-cost solution. Lower temperature of 260 degrees ...
READ MORE >>